Plastic extrusion for heat-sensitive plastics, PVC, and high-performance materials
Plastic extrusion for heat-sensitive plastics, PVC, and high-performance materials
Blog Article
Trick Advantages and Considerations of Carrying Out Plastic Extrusion in Your Jobs

Comprehending the Basics of Plastic Extrusion
Plastic extrusion, a staple in the manufacturing sector, is a procedure that involves melting raw plastic product and improving it into a continuous account. This account, once cooled, can be reduced right into preferred lengths or coiled for later usage. The appeal of plastic extrusion lies in its flexibility. A broad array of items, from piping to window structures, can be created. The procedure needs an extruder, an elaborate machine with a warmed barrel, a rotating screw, and a die at the end. The plastic product, in the form of pellets, is fed right into the extruder, where it's melted and forced with the die, taking its shape. The option of plastic and the design of the die determine the item's qualities.

The Economic Advantage of Plastic Extrusion
The economic benefit of plastic extrusion exists mostly in 2 locations: economical material production and advantageous production rates. With plastic extrusion, organizations can generate high volumes of material at a reduced price compared to other approaches. Additionally, the process boasts an outstanding manufacturing rate, considerably decreasing time and additional improving its economic practicality.
Economical Material Manufacturing
A considerable benefit of plastic extrusion is its exceptional cost-effectiveness. This manufacturing procedure enables continual, high-volume production with marginal waste, which equates right into lower prices. The raw materials made use of, usually plastic pellets, are relatively cost-effective compared to various other substances (plastic extrusion). The process itself calls for less power than many other manufacturing methods, additionally reducing expenses. In addition, the extrusion process enables for a high level of precision fit the plastic, lowering the need for expensive post-production changes or corrections. Furthermore, the durability and durability of extruded plastic items typically imply less need for substitutes, adding to long-lasting financial savings. All these factors make plastic extrusion a highly economical option for lots of jobs, using an eye-catching equilibrium in between expense and efficiency.
Beneficial Manufacturing Speeds
While maintaining the cost-effectiveness of the materials, one more significant benefit of plastic extrusion lies in its rapid production rates. This mix of speed, high quality, and cost-effectiveness underscores the significant economic advantage of executing plastic extrusion in different jobs.
Convenience and Modification: The Strengths of Plastic Extrusion
One of the prominent strengths of plastic extrusion depends on its versatility and customization potential. These qualities unlock to unlimited design opportunities, offering suppliers the capacity to customize items to particular needs. This heightened degree of modification not just improves product performance but also considerably boosts item originality.
Unrestricted Style Possibilities
Plastic extrusion shines in its capacity to use practically unlimited design opportunities. This technique provides liberty to produce detailed profiles and complex forms, an accomplishment hard to attain with other manufacture image source methods. Owing to the fluid nature of liquified plastic, the process is adaptable enough to yield a diverse variety of kinds, dimensions, and dimensions. The plastic can be controlled to match unique requirements, enabling the manufacturing of customized geometries and conference particular customer needs. Plastic extrusion can deal with a selection of plastic types, broadening its application scope. This adaptable strategy, therefore, serves a vast array of markets from construction to automobile, product packaging to electronic devices, and beyond. With plastic extrusion, the style opportunities are virtually unlimited.
Enhancing Product Individuality
The flexibility of plastic extrusion can considerably improve item uniqueness. This procedure enables developers to try out various shapes, dimensions, and shades, providing the liberty to develop one-of-a-kind items that attract he has a good point attention in the market. It is this customization that lends a distinct identification per item, differentiating it from its competitors.
In enhancement to its aesthetic benefits, the customizability of plastic extrusion also supplies useful advantages. Thus, plastic extrusion not just boosts item individuality however additionally its utility and bankability.
Design Limitations in Plastic Extrusion: What You Need to Know
Exactly how can design limitations potentially influence the process of plastic extrusion? While plastic extrusion is functional, design limitations can stop its advantages. Particular complex styles may not be practical due to the restrictions of the extrusion Get More Information procedure, potentially restricting the development of detailed profiles. The process is much less ideal for hollow or multi-chambered structures. Furthermore, the extrusion procedure might not always offer the preferred surface area coating, particularly for those requiring high gloss or optical clearness. Product option can additionally pose challenges, as not all polymers are appropriate for extrusion. High-temperature immune plastics, for circumstances, might offer difficulties. Understanding these restrictions is vital for reliable execution of plastic extrusion in your tasks. plastic extrusion.
Assessing the Environmental Impact of Plastic Extrusion
While recognizing design restrictions is a substantial aspect of plastic extrusion, it is similarly vital to consider its environmental ramifications. The procedure of plastic extrusion involves melting plastic materials, potentially launching harmful gases into the atmosphere. Making use of recycled plastic products in the extrusion process can decrease environmental effect.
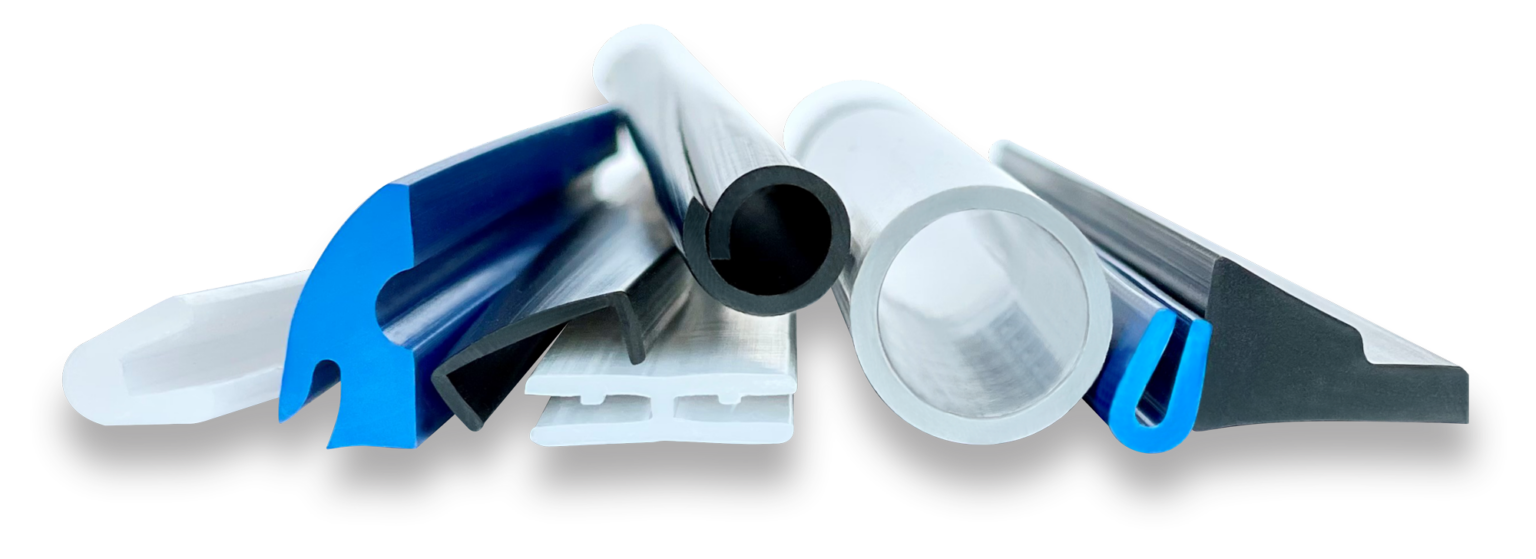
Case Research: Effective Projects Using Plastic Extrusion
Success tales in the field of plastic extrusion abound, showing both the convenience and efficiency of this production procedure. One noteworthy example is the development of PVC pipelines utilized in modern plumbing. This procedure involves melting plastic and developing it right into a continual tube, providing substantial cost and toughness benefits. Another successful instance is the production of plastic film for packaging and farming. Via extrusion, manufacturers can create extremely customizable, thin, and robust movies. Automotive sectors also benefit, utilizing extruded plastic for parts like trim or seals, improving lorry longevity. These instances illustrate plastic extrusion's important duty in numerous industries, vouching for its flexibility, cost-effectiveness, and reliable result.
Verdict
To conclude, plastic extrusion offers a economical and effective approach for generating complicated shapes with marginal waste. While it gives many advantages such as cost-effectiveness and flexibility, it's essential to consider possible style limitations and ecological impacts. Executing eco-friendly or recycled materials can mitigate these problems, enhancing sustainability. Including plastic extrusion into tasks can cause successful end results, as evidenced by countless study.
Plastic extrusion, a staple in the manufacturing market, is a procedure that entails melting raw plastic material and reshaping it right into a continuous profile. Plastic extrusion can manage a variety of plastic kinds, expanding its application range.Exactly how can design restrictions possibly influence the process of plastic extrusion? The process of plastic extrusion includes melting plastic products, possibly releasing harmful gases into the setting. Making use of recycled plastic materials in the extrusion process can decrease environmental effect.
Report this page